Blog
What's a Fair Price For a General Biomedical Service Contract? (Part 1)
Posted by
onPart 1
The Fundamentals of a General Biomedical Contract
Everybody hates paying bills! Especially service bills that are a result of mandatory regulations. At least when you pay an invoice for a product, you have something tangible to show for it. Biomedical service bills for "preventative maintenance" are a mystery to many and an expensive reality healthcare providers, obligated to comply with CMS and voluntary accreditation agencies.
The million dollar question is; what do you get and how much should it cost? In order to answer this question, you must understand the basics and principles of a "general biomedical service contract." Without this information, your service contract will remain a mystery.
Simply put, all electric medical devices must be checked at predetermined time intervals, according to manufacturer recommendations, or according to FDA risk levels, whichever is greater. In reality, most devices need to be checked only once a year with a few needing to be checked twice a year or quarterly. What do I mean by "checked?" All devices must have an electrical safety leakage test performed, once a year. This is commonly referred to as a “safety check” and many healthcare providers assume this to mean that a device is working according to manufacturer specifications or safe to use. A “safety check” just means that a device is properly grounded and there is no excess electrical leakage that could cause a spark or shock a person. In addition, only “medical devices” can be safety checked as they must meet certain design criteria. In order to ensure functionality, a device must be “performance tested,” according to its specific characteristics. Some devices need output or calibration checks in order to verify they are performing according to OEM/ manufacturer specifications. A calibration or output check would typically be performed on vital signs monitors, defibrillators or electrocautery devices. If they don’t meet the output criteria they will require calibration. Some devices may also require parts be changed or kits installed, at predetermined time or hourly usage intervals, such as autoclaves and anesthesia machines. In addition to verifying that all devices are checked accordingly, records must be kept, proving each device meets its specific performance criteria. All of this work must be documented and formatted into a “Biomedical Records Report.” This report should contain the following information:
- Detailed Inventory Records: This should list every device that requires biomedical maintenance with manufacturer, model number, serial number and a unique control or asset number.
- Last Test Date Records: This report should show the last time a device was tested, as well as basic performance data, related to the device in your inventory.
- Next Test Date Records: This report should show the next scheduled test date for each device in your equipment inventory.
- Additional Documentation: In addition to the three basic reports, already mentioned, it’s a good idea to include in your biomedical report binder, a copy of your service provider’s general liability insurance, certification of technical capability and a copy of your service contract, as proof of service commitment.
- Work Orders: Any time a device is tested or repaired, a work order should be opened, by your biomedical service provider. The work order contains the detailed technical data and information related to that particular device. Because the information is so voluminous, its impractical to keep it in printed format. Regardless, it should be made available to you by your service provider if needed or requested by an inspector or surveyor.
- Service Decals: It’s important that all your devices, under contract, be tagged with an inspection decal that’s highly visible. The tag itself should indicate the testing and performance condition, of that device, with just a quick glance.
The time needed for locating, testing, calibrating and reporting, needed to fulfill a service contract, would cause you to assume that time is the key component in calculating cost. However, you may be surprised to learn that many companies use very formulas where they assign a cost, per device, and then simply multiply the amount of devices you own, by this set cost. This results in a charge factored by data that's not tailored to your facility. The only way to fairly calculate the cost of a contract is by the amount of time needed to do the work, multiplied by a discounted hourly rate.
Why a discounted rate? By signing a contract you're guaranteeing the service provider a certain amount of work, over a period of time, and that merits an incentive. The incentive should be a better rate than you'd receive if you were simply hiring them hourly. This incentive is the difference between paying a fair and reasonable amount for a general biomedical contract or paying an amount that will make you feel like you're being robbed. Simply put, you’re pre-paying for work that needs to be done on a scheduled basis and that’s what should qualify you for a reduced rate.
To Be Continued….
Selling Your Used Medical Equipment
Most health care facilities have little idea of what their equipment is worth, when they want to sell it. Unfortunately, there's no such thing as a "Blue Book" of medical equipment prices.However, we do have the internet and it can be a very valuable tool, in terms of researching the value of your equipment. My [...]
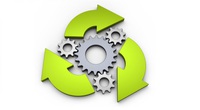
Used, refurbished; what does it all mean?
For many vendors, used and refurbished are one and the same. The term "refurbished" has been used in the medical industry for the past 50 years. The FDA does not define "refurbished" but the state of Texas, Department of Health, does regulate the "medical salvage" industry and defines "refurbished" as equipment that has been brought [...]